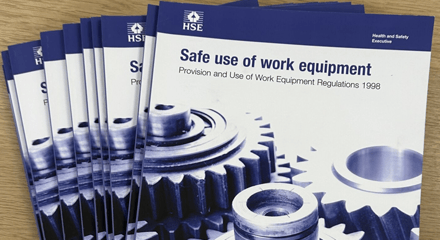
Is PUWER necessary?
If your work equipment is listed in Regulation 2 of PUWER, then YES, you do need to carryout a PUWER assessment and the PUWER assessments must be carried out by a competent person.
We are often ask that 'as our new machine is CE Marked, do we really need to carry out a PUWER assessment?' If you split it down, CE Marking is legislation for manufacturers and PUWER is legislation for the end users, whether a company or individual. PUWER (or the Provision and Use of Work Equipment Regulations) has a more broad scope when compared to CE Marking.
If a machine has been CE Marked in accordance with the Machinery Directive, then a Machinery Design Risk Assessment should have completed and the necessary safeguarding's installed to reduce risk to an acceptable level. Regulation 10 of PUWER address Conformity with Community requirements, however there are a lot more regulations that need to be satisfied and which are assessed during a PUWER assessment. If you are not familiar with the PUWER regulations, then the PUWER ACOP (Approved Code of Practice) is a good place to start. The PUWER ACOP is available for free download from the HSE (Health and Safety Executives) website: Safe use of work equipment. Provision and Use of Work Equipment Regulations 1998. Approved Code of Practice and guidance L22
The Provision and Use of Work Equipment Regulations 1998, often abbreviated to PUWER, place duties on people and companies who own, operate or have control over work equipment. PUWER also places responsibilities on businesses and organisations whose employees use work equipment, whether owned by them or not.
PUWER requires that equipment provided for use at work is:
- suitable for the intended use
- safe for use, maintained in a safe condition and inspected to ensure it is correctly installed and does not subsequently deteriorate
- used only by people who have received adequate information, instruction and training
- accompanied by suitable health and safety measures, such as protective devices and controls. These will normally include emergency stop devices, adequate means of isolation from sources of energy, clearly visible markings and warning devices
- used in accordance with specific requirements, for mobile work equipment and power presses
Some work equipment is subject to other health and safety legislation in addition to PUWER. For example, lifting equipment must also meet the requirements of LOLER, pressure equipment must meet the Pressure Systems Safety Regulations.
Selection and conformity
Work equipment must be suitable for the purpose for which it is used or provided, and used only for operations for which it is suitable. In selecting work equipment, employers must take account of:
- the working conditions and risk to health and safety from the premises it will be used in
- who will use the equipment?
- the work equipment itself
New work equipment should conform to any essential requirements for safety applicable to it through European product supply law, such as the Machinery Directive.
Inspection of work equipment
The purpose of an inspection is to identify whether work equipment can be operated, adjusted and maintained safely – with any deterioration detected and remedied before it results in a health and safety risk. Not all work equipment needs formal inspection to ensure safety and, in many cases, a quick visual check before use will be sufficient. However, inspection is necessary for any equipment where significant risks to health and safety may arise from incorrect installation, reinstallation, deterioration or any other circumstances. The need for inspection and inspection frequencies should be determined through risk assessment.
Maintenance of work equipment
PUWER requires that: all work equipment be maintained in an efficient state, in efficient order and in good repair; where any machinery has a maintenance log, the log is kept up to date; and that maintenance operations on work equipment can be carried out safely.
Training and competence
All people using equipment at work must be adequately trained to ensure health and safety in its use, supervision or management. Some work activities require detailed formal training but, for most everyday activities involving work equipment, adequate training can be delivered in-house using the manufacturer's instructions and the background knowledge / skills of more experienced workers and managers.
People should be competent for the work they undertake. Training – along with knowledge, experience and skill – helps develop such competence. However, competence may (in some cases) necessarily include medical fitness and physical / mental aptitude for the activity.
Mobile work equipment
Mobile work equipment - including self-propelled, remote-controlled work equipment - is subject to specific requirements in addition to the requirements for normal work equipment, which cover:
- the suitability of equipment used for carrying people
- the minimising of rollover risk
- the provision of equipment to restrain or protect people (in the event of rollover or overturn)
- the control of the equipment, including operator vision and lighting (where required for safety)
Manufacture and supply of new work equipment
All new work equipment must by design, construction and supply comply with one or more legal requirements when first placed on the market or put into service, to ensure that they can be used safely and without harm.
For most new products these requirements originate in EU Directives which set out common minimum European requirements for health and safety, including CE marking.
The array of European Directives requirements is vast but primarily, concerned with the design, manufacture and supply of new products, particularly machinery, including:
- designing and building for safety
- assessing product conformity
- demonstrating product compliance
- providing users with relevant information
Second-hand (re-supplied) products
Anyone supplying second-hand equipment for use at work must ensure, so far as reasonably practicable, that it is safe and without risks to health. This applies at all times when the equipment is being set, used, cleaned or maintained by a person at work. Adequate information should also be provided concerning the intended use of the equipment.
Where the second-hand equipment is in scope of one of the European product supply Directives and has not previously been put into service in the European Economic Area (EEA), or placed on the market of the EEA, the person importing it into the EEA must meet the conformity assessment requirements of the relevant European Directives, including CE marking.
The term "sold as seen" or similar cannot be used to avoid these legal responsibilities.
Refurbished and modified machinery
Some machinery provided for use at work is refurbished or modified, sometimes without change of ownership, but also often prior to re-supply as second-hand equipment.
The extent of the changes made to the original machinery, together with its provenance, can result in new legal obligations on the owner, user or person undertaking such work.
In some cases where machinery has been so transformed or substantially rebuilt it may have to be considered as new machinery and so subject to the conformity assessment and CE marking requirements of the Machinery Directive even if originally compliant and CE marked when first placed on the market.
However, refurbishment, even if very substantial, where parts are replaced with new similar versions (like for like etc) do not require re-CE marking.
What next?
If you would like to discuss your responsibilities under PUWER and how to facilitate PUWER inspections, then please do not hesitate to contact us.